Producing Titanium Castings
The titanium casting process requires that special techniques be used. This is due to its reactivity in the molten stage, high melting temperature and low mould filling properties.
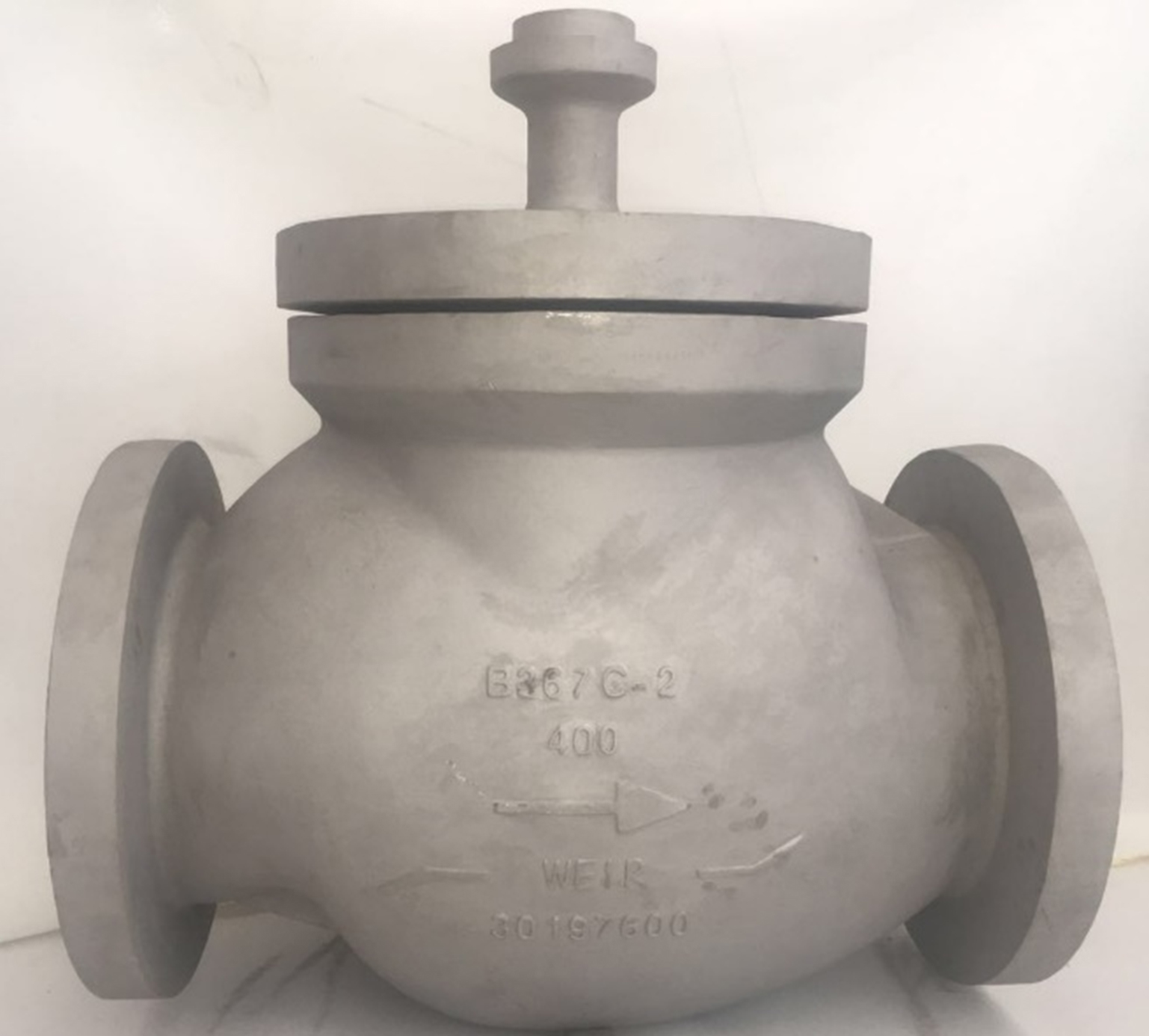
Machined graphite or investment technology
We offer castings produced by either machined graphite or investment technology. The choice of casting route depends on the requirements to quantity, surface finish, configuration and dimensional accuracy of components.
Investment casting technology is generally used for large quantities with close dimensional tolerances and complex shapes, and involves higher tooling- and fabrication- costs.
Castings manufactured using machined graphite mould or investment technology are generally 10 % lighter in weight compared to traditional sand mould technology using wooden patterns.
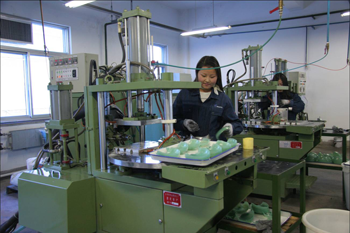
Lost foam technology
Middle and small size castings of complex shape are produced using lost foam technology. The patterns are produced by ALBA pattern shop.
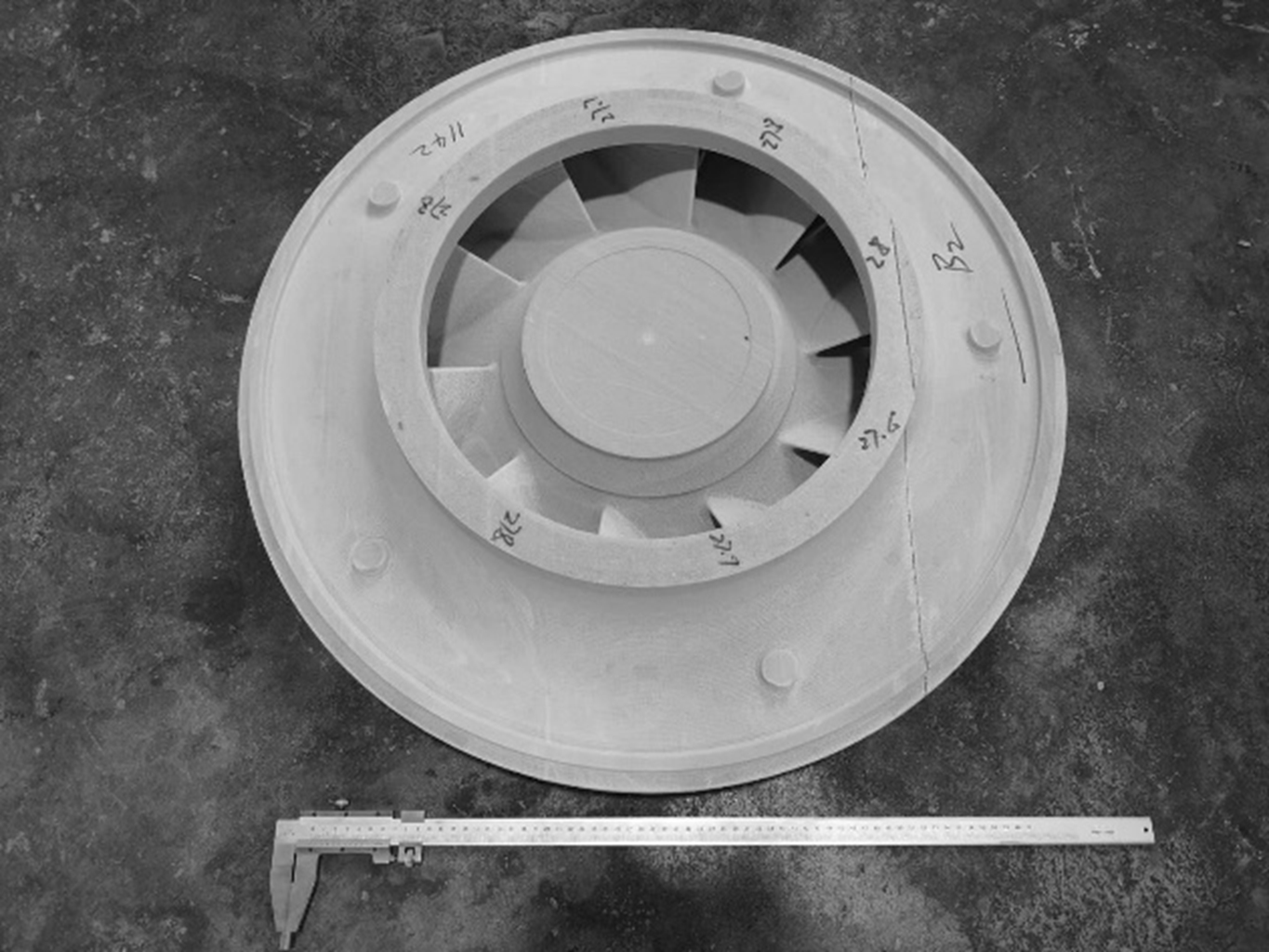
Making the mould
The mould must be relatively inert when in contact with the molten titanium metal. The type of mould material and binder used has a significant impact on the surface quality and the alpha case thickness of the casting. The thicker alpha case, the higher risk for serious failure.
The graphite moulds used by ALBA gives a typical alpha case thickness of 50 - 70 micron.
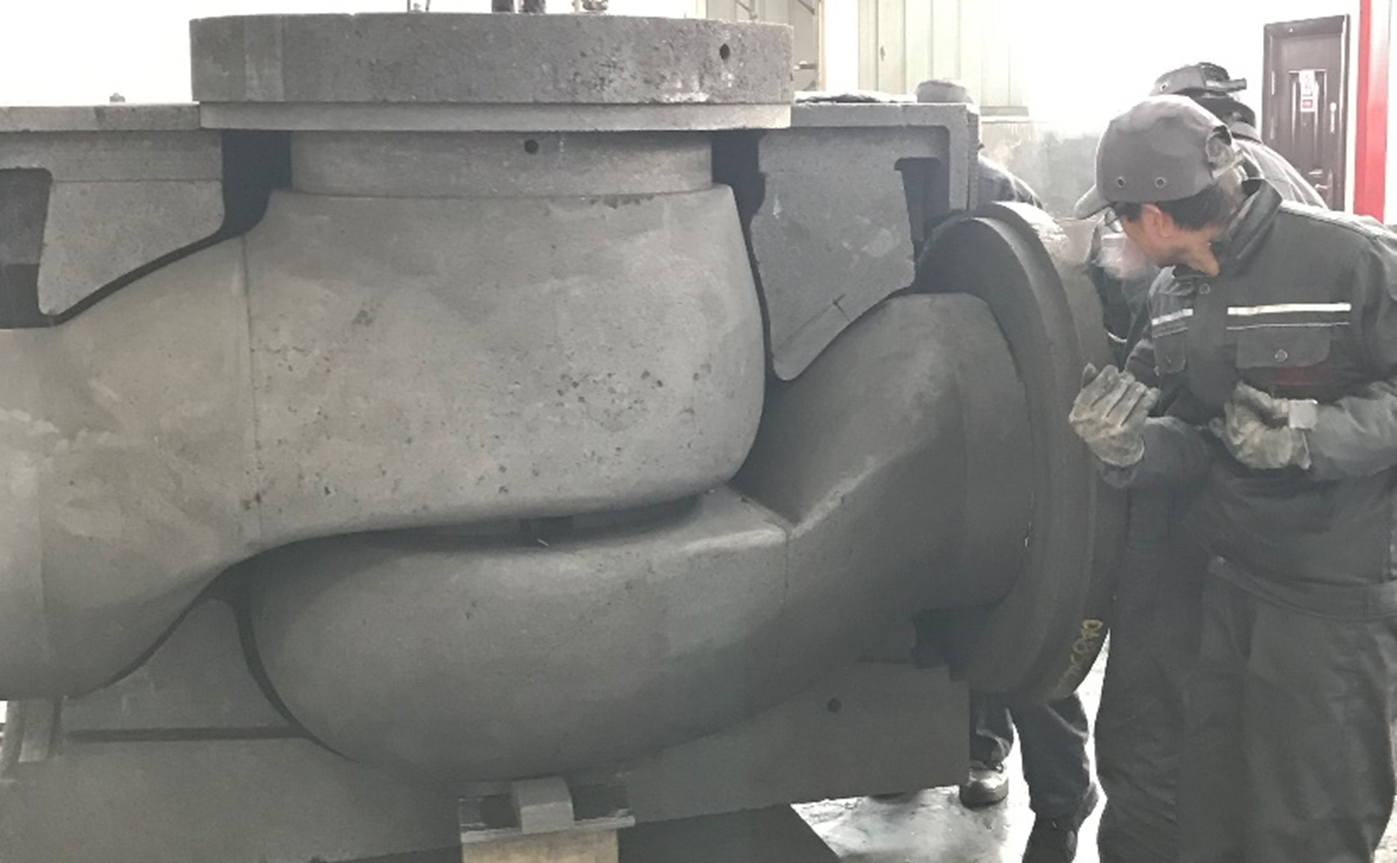
Melting and pouring
Titanium castings are produced in vacuum consumable-arc electrode furnaces with semi-automatic melting and pouring operations. The crucibles are either graphite or copper water-cooled crucibles.
The melting capacity ranges from 80 kg to 3500 kg liquid titanium, enabling us to produce castings with commercial weights from a few grams up to 1500 kg.
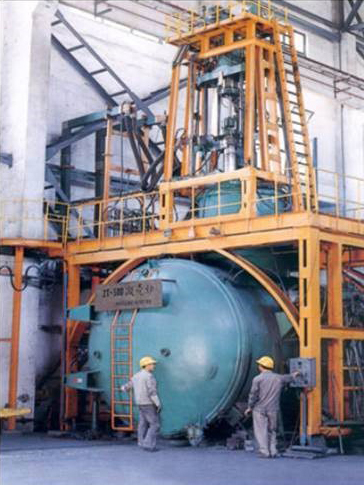
Inspection and Quality control
Castings are manufactured in accordance with ASTM B367 under the guidance of ALBA's engineers and qualified inspectors.
Our NDT operators are all certified in accordance with PED / ISO 9712 (former EN473) and ASME Code.
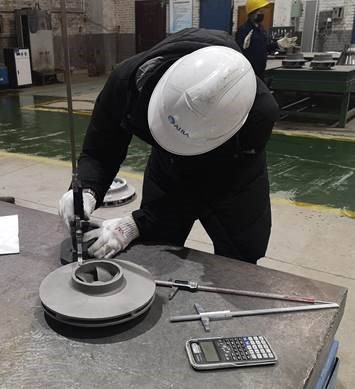
Weld repair
Our certified welders can repair any surface or sub-surface defects. The welding method used is GTAW with pure argon as protective gas. Welding procedures are qualified to American ASME IX and European PED EN-15614/EN9606.
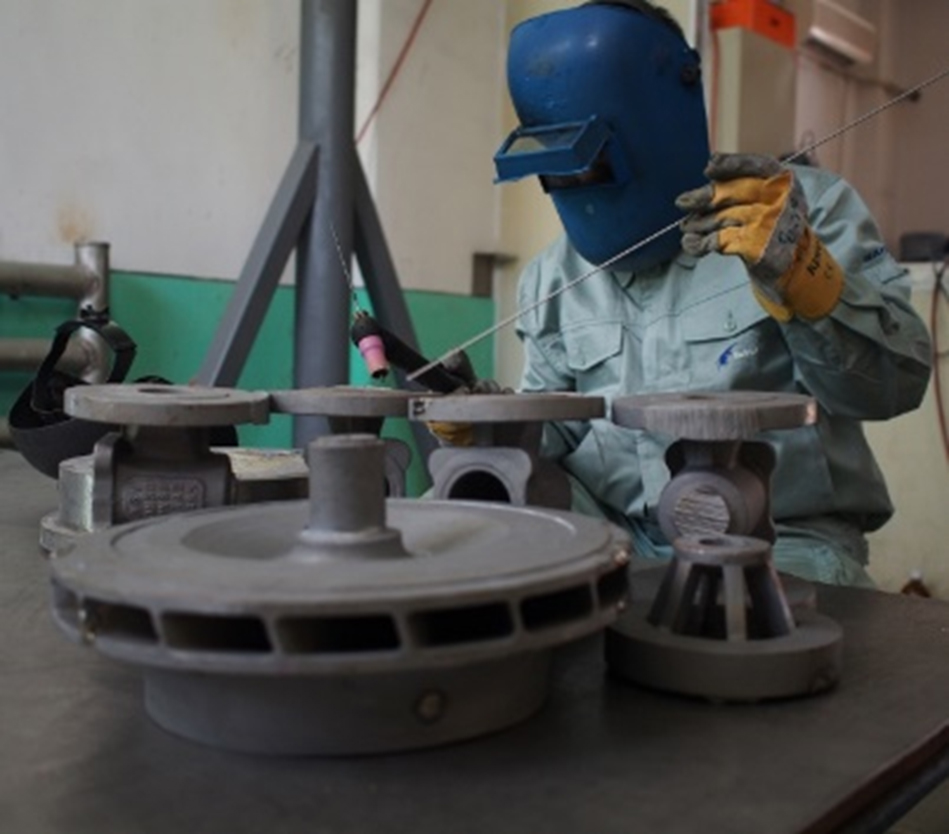
Finishing operations
Castings are as standard delivered in pickled and cleaned condition.
We offer finish machined castings.
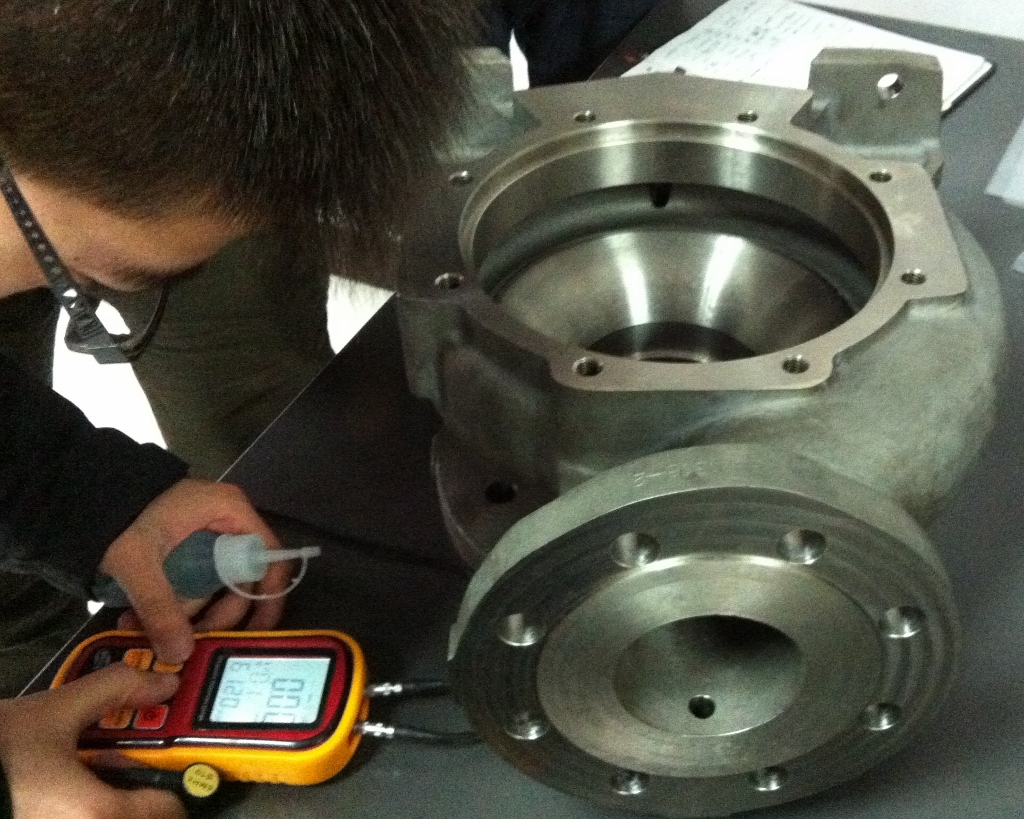